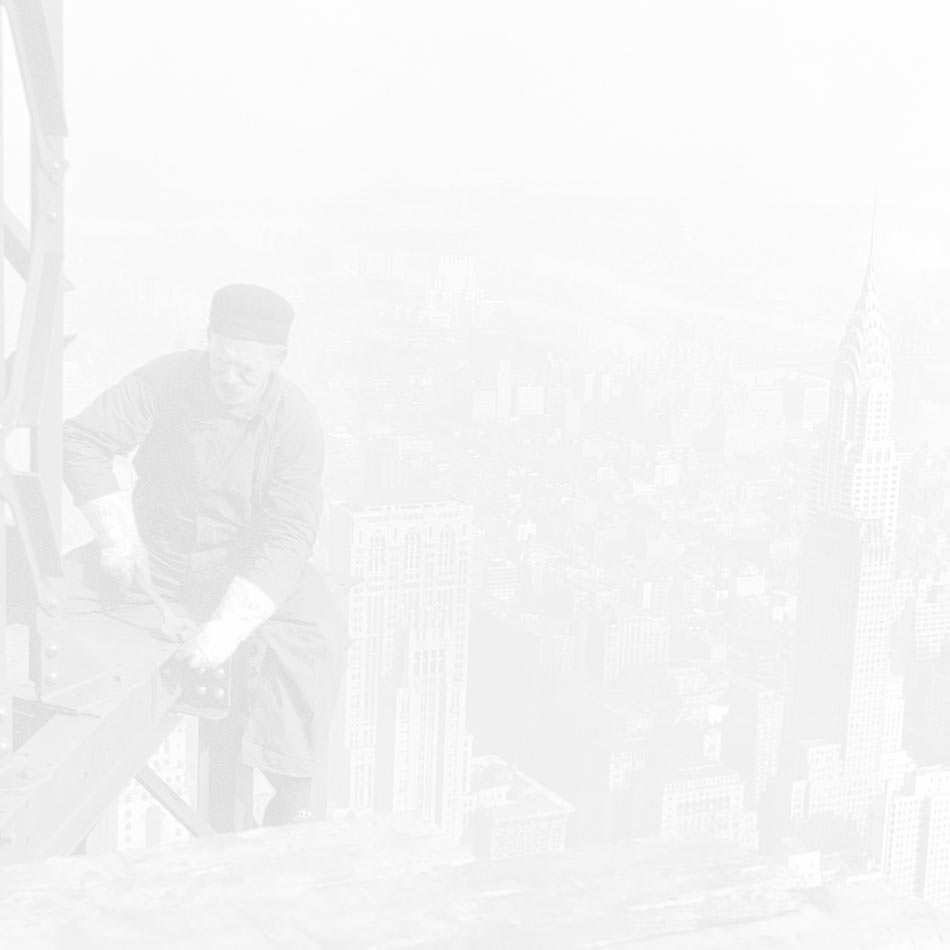
SynSol
Introduction
Reinforced concrete (RC), due to its favourable mechanical behaviour, is one of the most widely used materials in the construction industry nowadays. However, RC produces extremely high CO2 emissions, making the construction industry a leader in greenhouse gas emissions. The elements of the RC are cement concrete and steel reinforcement. These elements can be replaced with new materials, but due to the lack of knowledge and guidelines these are less common. Significant reductions in the environmental footprint of RC structures will necessitate the use of new, innovative methods in materials, constructing and design as well. Even a small change in the CO2 footprint of RC material can yield high results.
Our solution
By rethinking and optimising RC structures the CO2 footprint can be significantly reduced. Our optimisation plan would take place on three levels: materials, structures, and design optimisation.
During the optimisation of materials, we would research and investigate concretes made from cements with low CO2 emissions, or their alternatives. Our study would also cover the testing of CO2-binding concretes, their applicability and strength characteristics. In the field of reinforcements, the replacement of steel bars used in concrete with fiber reinforced polymers (FRP) and synthetic macro fiber reinforcement (FRC) would be investigated. With regard to materials, it is also important to consider the possibilities for recycling existing materials. The combined use of these new materials is at a state-of-the-art level.
During the optimisation of structures, we would deal with a geometric optimisation fit for these new types of concrete and reinforcements. The optimisation would keep the price of the construction with significant material savings.
Analytical material models can be achieved from the test results, and using these would result in optimised design and lower CO2 emissions, while strictly meeting the requirements of the standard and the required level of safety.
The main research area of our company is testing, researching and designing fiber-reinforced and FRP-reinforced concretes. Our company won a EUROSTAR tender in 2017 for developing a calculation method for fiber-reinforced concretes. Our research field is testing and providing design methods for FRC and FRP materials. Using our knowledge, we had the opportunity to participate in both Hungarian and foreign projects, where the task was to design and/or optimise RC structures. During these designs, we mostly reinforced the given structure by using fiber reinforcements and FRP bars, and we reduced the amount of the concrete as well.
Concrete industry
The most significant segment in the construction industry is the concrete industry. A significant part of the load-bearing structures of construction works is made from reinforced concrete, but concrete can be found in almost all types of buildings.
In Europe, the standards required for calculating concrete structures can be found in EUROCODE. The fields which are not covered by the standard are designed based on guidelines or technical recommendations such as FRC and FRP.
Changing and innovating the design standards is a long process, but creating new, more advanced materials by satisfying the requirements is faster, so joining the public knowlege is also an easier step. Our company is not new in the concrete industry, thus the connection is already given.
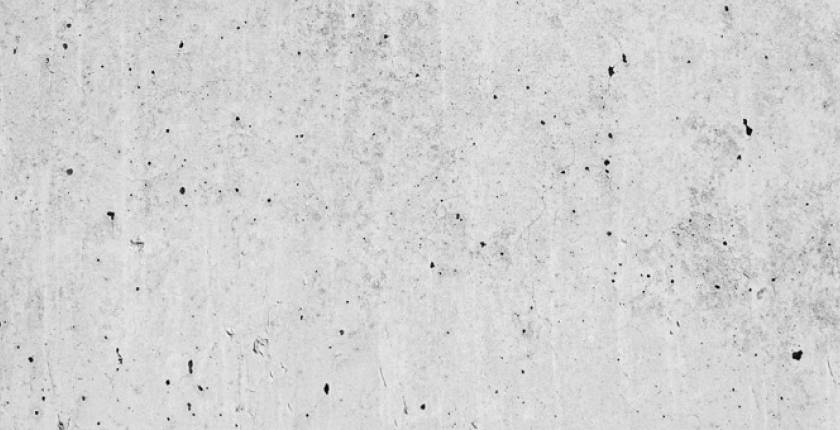
Motivation
Our company and its members are interested and involved in sustainable development. One frequent obstacle is separating the design process and local errors in them, which accumulate during the process. By keeping this calculation process in one hand, overestimated safety can be reduced. Our company undertakes the complete maintenance of this process: the design and testing of concrete, the determination of material parameters, and then the calculation and optimisation of the structure. In the whole process, results can be achieved not only by optimising the sub-processes, but also by coordinating the whole process. In our company, it is important that all members are aware of the sub-processes, while at the same time there are people responsible for each task. With this structure we have created the foundation of our company, which are Laboratory – Research – Design, closely connected to each other.
Our company has been present on the concrete market for more than 10 years, due with our specialization it is fair to say that we are a recognized designing and consulting company both inside and outside of the country. Abstracts of our references can be found on our website, including in-situ and precast concrete, from track slabs to shotcrete or precast TBM tunnels. The bases of our company were designs based on our own research and studies. A numerical material model for fiber-reinforced concrete can also be found in different guidelines. In Hungary, the first track slab reinforced with only synthetic fibers was made in Hungary in Szeged, and then in many places in Europe and beyond, such as London, Tallinn, St Petersburg. As a company and as members of the company, we are both successful and determined in the development and environmental-friendly use of concrete material and towards the structures made from it.
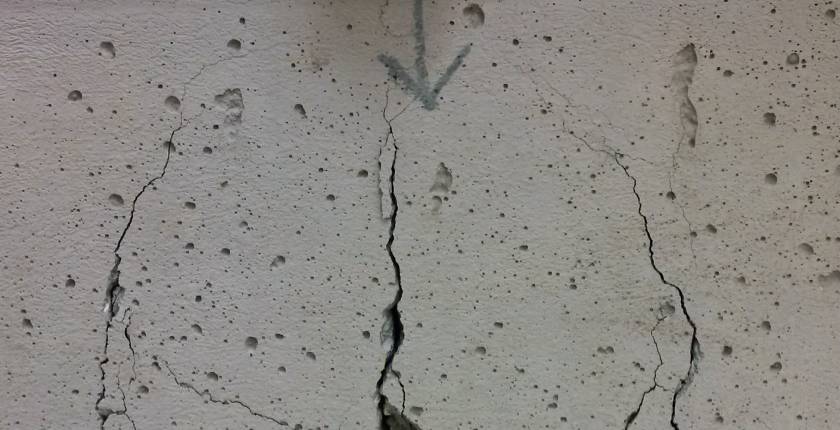
STEP 1. Comparison study of GFRP
The purpose of the experiment was to investigate the effect of the different internationally recognized Fibre Reinforced Polymer (FRP) rebars in concrete beams. The research contains laboratory experiment and Finite Element Analysis (FEA) . The final goal was to compare the bending capacity of different FRP rebars in concrete beams.
After the preliminary laboratory tests finite element material models were developed for each bar, which follow exactly the behavior of the noticed bar in concrete. To produce the bending failure (which causes the rupture of the FRP bars) in the concrete beams steel stirrups were applied to bear the shear stresses.
Test specimens
Tested beams: 1100 mm long, 160 mm high, 100 mm wide concrete beams as shown in Pic.1.
Concrete strength class: C50/60 according to Eurocode 1992-1-1.
More details: FRP_report
Publication on this topic: FRP_publication
STEP 2. Comparison study of cement types
The cement industry is the second-largest industrial emitter of CO2, and it is responsible for almost 8% of the total global emission. To stop global warming, we need to solve this problem. We need innovation in both cement production and carbon utilisation. In producing 1,000 kg of cement, you emit 1,000 kg CO2 into the atmosphere. Being fully aware of this fact, we try to find the best CO2 reduced cement, which is not only good for the environment but also its strength and durability are even better than traditional cement.