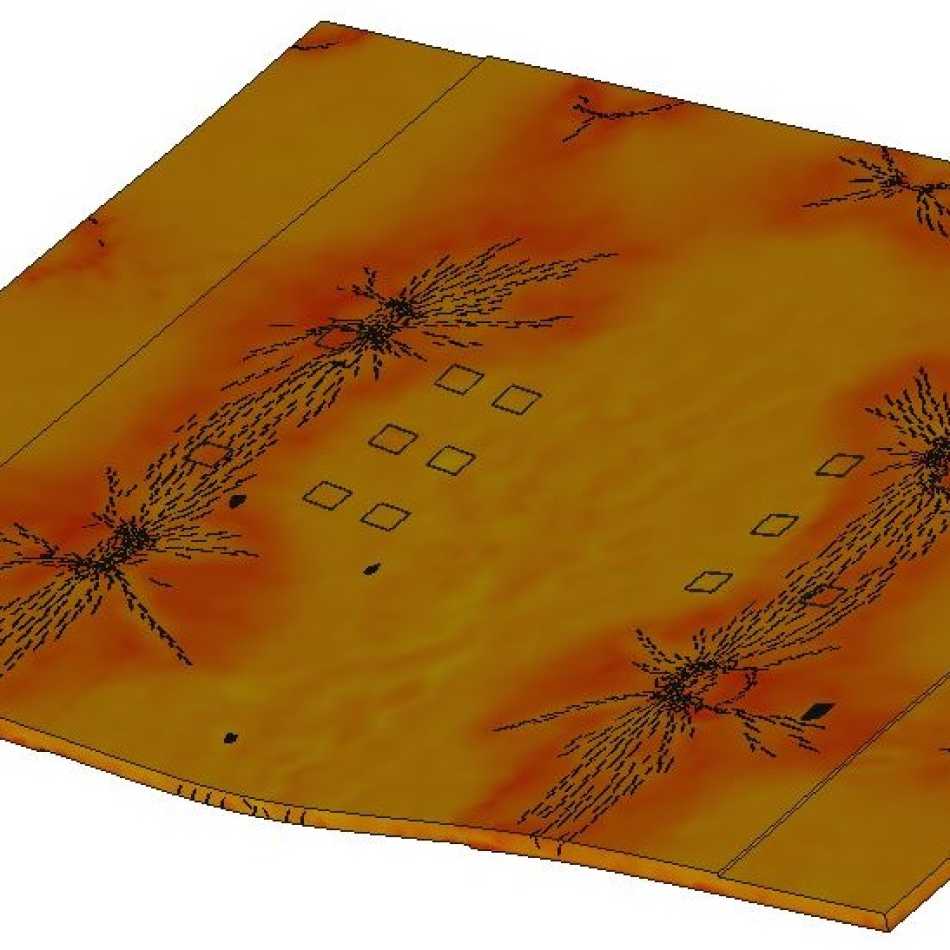
FEA
In our structural analyses at JKP Static Ltd., we utilize ATENA Finite Element Analysis (FEA) software [1], which is specifically designed for the simulation of concrete, reinforced concrete, and fiber-reinforced concrete structures. ATENA is widely recognized for its accuracy in modeling the behavior of brittle materials and is particularly well-suited for projects requiring detailed analysis of structural performance under complex loading conditions.
ATENA belongs to the class of advanced analysis software such as ABAQUS and ANSYS, but it focuses specifically on the intricacies of reinforced concrete structures. Its development is based on the Finite Element Method (FEM) and features material models that accurately simulate the nonlinear behavior of concrete, such as cracking, crushing, and post-cracking behavior.
Key Features of ATENA in Structural Analysis
1. Concrete in compression and in tension
One of the fundamental aspects of modeling concrete in ATENA is its use of a combined failure surface model. The software utilizes a William-Menétrey failure surface for compression and a Rankine surface for tension, which together allow for a realistic depiction of concrete behavior under stress [2, 3]. For post-cracking behavior, ATENA applies the Hordijk curve [4] in conjunction with the crack band method [5], ensuring that the quasi-brittle characteristics of concrete are appropriately modeled.
William-Menétrey combined failure surface [2]
Hordijk curve [4]
2. Fiber-Reinforced Concrete (FRC) Modeling
The Modified Fracture Energy Method (MFEM) for modeling fiber-reinforced concrete (FRC), originally published in the PhD thesis of Dr. Peter Karoly Juhasz [6], has been implemented into ATENA through the FibreLAB project [7]. This method integrates fibers into the material model, modifying the fracture energy curve to reflect the enhanced performance during crack formation and opening. This extension of the standard model allows for a more accurate analysis of structures that incorporate synthetic fibers. This design method is also recommended by the ITAtech (Design guidance for precast fibre reinforced concrete segments).
Material model parameter for FRC
3. Crack Visualization and Analysis
ATENA provides real-time visualization of cracks, enabling the discrete representation of crack paths and the calculation of crack width and direction. This feature is particularly valuable in research and practice, where the progression of cracks under loading conditions can provide critical insights into the behavior and durability of concrete structures.
Crack visualization in ATENA
4. Detailed Reinforcement Modeling
The software also allows for discrete modeling of reinforcement, wherein reinforcing bars are modeled as line elements in their precise location. This approach permits a more accurate representation of the interaction between concrete and reinforcement, especially under complex loading conditions. It also aids in the optimization of reinforcement layouts by analyzing the effectiveness of individual bars in the load-bearing process.
Verification and Validation of ATENA
ATENA has undergone extensive verification through both numerical benchmarks and laboratory tests. These verifications have consistently demonstrated good agreement between ATENA’s numerical simulations and experimental results, confirming its capability to model real-world behavior accurately.
1. Toronto Shear Test
One notable example of ATENA’s reliability is its participation in the Toronto shear test competition [5], where it was used to predict the shear capacity of large-scale concrete wall panels. ATENA’s prediction of the shear load capacity was within an 8% margin of error compared to actual test results, highlighting its ability to accurately simulate complex shear behavior in reinforced concrete. Read publication.
2. Shanghai Metro Tunnel Extension
In collaboration with JKP Static Ltd., ATENA was applied to simulate the load-displacement behavior of the Shanghai Metro Tunnel extension under full-scale laboratory testing [8]. The results from ATENA’s simulation closely matched the experimental data, reinforcing its value in large-scale infrastructure projects requiring high precision in design and optimization. Read publication.
Real scale laboratory test of Shanghai Metro TBM Tunnel
Load-deflection diagram of test and ATENA analysis
3. PCAT Precast Tramline Project
In collaboration with PreCast Advanced Track, JKP Static Ltd. was tasked with the finite element modeling of a macro synthetic fibre-reinforced concrete slab structure designed for railway construction and repair [9]. During the design process, ATENA was used to model the static, dynamic, and fatigue loads of the structure. The slab was subjected to early age verification for de-moulding, lifting, transport, and final installation.
Real-scale testing was conducted by AECOM, where the structure was placed in a concrete pool filled with compacted sand. Using a Rail Trackform Stiffness Tester (RTST), displacements were measured, and ATENA’s finite element models closely matched the test results. This project demonstrated ATENA’s ability to accurately model complex railway infrastructure under various loading conditions. Read publication.
Rail Trackform Stiffness Tester
Displacement result of test and FEA
4. Blind Simulation Competition (BSC) on Punching Shear
JKP Static Ltd. participated in the 3rd Blind Simulation Competition, which aimed to assess the performance of FEA models in predicting punching shear failure in fiber-reinforced concrete slabs [10].
The competition involved predicting the behavior of two real-size prototypes subjected to progressive collapse loads. ATENA’s simulation, which used a smeared crack model (SCM), placed JKP Static Ltd. in second place among 26 international participants, with results that closely matched the experimental data. The competition demonstrated ATENA’s capacity to model complex failure modes and accurately predict post-peak load-carrying capacity in fibre-reinforced structures. Read publication.
3D model
Red: prediction of JKP Blue: test
5. Debrecen Stadium Grandstand Modeling
ATENA was also utilized in the design and analysis of the Debrecen Stadium grandstand elements, where the software’s simulation of fibre-reinforced concrete elements demonstrated close alignment with full-scale laboratory tests. This validation is essential for understanding the behavior of prestressed, fibre-reinforced elements under bending and shear loads [11]. Read publication.
Load-deflection of test and FEA
Crack width of test and FEA
6. Manholes exposed to railway loads
At a railway-side manhole, MÁV (Hungarian Railways) required a full-scale test to meet their stringent regulatory standards. The testing involved two manholes: one made of plain concrete and the other reinforced with synthetic fibres. This real-scale loading test served multiple purposes. It was not only a validation exercise for the ATENA finite element software used in the design but also a practical demonstration of the enhanced ductility provided by fibre-reinforced concrete [12]. Read publication.
Results of test and FEA
Applications in Research and Structural Optimization
ATENA is widely used in academic research and industrial projects for its ability to simulate the behavior of concrete under various load conditions, including dynamic and fatigue loads. In addition to its widespread use in fiber-reinforced concrete analysis, ATENA’s flexibility in material modeling allows researchers to incorporate user-defined material properties, making it highly applicable for experimental verification and the study of novel materials.
At JKP Static Ltd., ATENA has played a central role in projects like the development of the PCAT precast tramline slab and the Shanghai Metro Tunnel, where its accurate modeling of concrete and fibre-reinforced structures has contributed to design optimizations that enhance both performance and sustainability.
Conclusion
ATENA’s combination of advanced material models, precise crack visualization, and its ability to model reinforcement discretely makes it an invaluable tool for both research and practical applications. Its capabilities have been validated in numerous benchmark studies and real-world projects, ensuring that the software provides reliable results that can be trusted in both academic and professional settings.
At JKP Static Ltd., we continue to use ATENA not only for our own design and analysis projects but also to contribute to the advancement of structural engineering knowledge, ensuring that our results are both accurate and aligned with the latest industry standards.
References
[1] https://www.cervenka.cz/products/atena/
[2] Cervenka, J. and Papanikolaou, V.K. (2008). Three dimensional combined fracture-plastic material model for concrete. International Journal of Plasticity (24) pp. 2192–2220. https://doi.org/10.1016/j.ijplas.2008.01.004
[3] Menetrey, P. and Willam, K.J. (1995). Triaxial failure criterion for concrete and its generalization. ACI Structural Journal (92/3) pp. 311–318, May 1995. http://dx.doi.org/10.14359/1132.
[4] Hordijk, D.A. (1991). Local approach to fatigue of concrete. Doctoral thesis. Delft University of Technology, The Netherlands, p. 70.
[5] Bažant, Z.P., Oh, B.H. (1983) Crack band theory for fracture of concrete. Materials and Structures (16) pp. 155–177. https://doi.org/10.1007/BF02486267
[10] Barros, J.A.O. etal (2024). Blind competition on the numerical simulation of slabs reinforced with conventional flexural reinforcement and fibers subjected to punching loading configuration. Structural Concrete. DOI: 10.1002/suco.202400061